以数字科技为驱动力 奇瑞捷豹路虎铸就智能制造典范
今年全国两会政府工作报告在强调深入实施创新驱动发展战略的同时,就加强数字中国建设整体布局、促进数字经济发展等方面做出了部署。5G、工业互联网、关键软硬件……从关键词中就可以看出数字经济发展新趋势,数字化转型已成为各行各业的重点。
而随着数字化浪潮的持续深入,大数据、人工智能与云计算等技术的日益演进,造车过程也不例外。基于对中国市场的洞察和本土研发的经验积累,奇瑞捷豹路虎率先应用工业互联网,借助数字化技术手段,在经济数字化转型中抢抓先机,坚定步伐走在行业智能制造前列。
数据先行,率先探索工业互联网
早在成立之初,奇瑞捷豹路虎便积极推进数字化落地,将传统汽车制造业与智能制造优势的融会贯通,树立了汽车行业智能制造的新标杆。作为全球统一生产标准建设的全球样板工厂,奇瑞捷豹路虎常熟生产基地率先应用工业互联网,实现“人、机、网、场”的互联互通,以生产过程的可感知、可预测、可控制,使整车四大工艺车间的智能化程度达到全球领先水平。
常熟生产基地焊装车间
奇瑞捷豹路虎是业界首个启用基于“端到端”制造执行系统MES的企业,实现了订单管理、制造管理、质量管理、物流拉动、防错管理、追溯管理等功能的全覆盖。集高适应性、高集成性于一体的全功能型制造执行系统MES,可以通过工业大数据网络实时监控生产及设备信息,精确追溯每一台车的制造数据,实现生产质量问题的大数据分析,并利用问题解决及预防系统AIMS对产品设计进行改善。加上高度自动化、柔性化以及与整体工业物联网连接的物流执行系统LES,奇瑞捷豹路虎能够确保准时交付世界一流品质的产品。
常熟生产基地发动机工厂高度柔性化生产
为满足捷豹和路虎两个豪华汽车品牌消费者的个性化定制需求,以数字化赋能智能制造,奇瑞捷豹路虎已经实现量身定制的订单生产,可轻松处理30万种个性化选装配置。当客户选好相关配置,系统会生成完全定制化的整车SuperBOM。订单由位于英国的全球经销商订购系统收集并汇总,而后通过PLO订单排产(Pipeline Ordering)系统发送到覆盖研发、制造、物流、财务、采购、销售及售后的SAP系统。凭借生产过程中的“一车一单”,奇瑞捷豹路虎能够高效、精准地执行复杂多样的订单生产。
全新XFL驶下常熟生产基地生产线
面对电动化的时代浪潮,为确保新能源汽车的生产“智”造,常熟生产基地还进一步深化工业互联网的应用,新增高压电池、电机、控制器、高压线束等高压零部件追溯系统,确保十大类高压零部件制造全程追溯。不仅如此,奇瑞捷豹路虎搭建了与工厂智能物流系统联动的总装零件选取防错系统,进一步降低劳动强度和错误率。为了进一步保证产品的硬核品质,除常规车辆装配控制点之外,常熟生产基地新增69个伺服工具的控制程序,对插电混动车型专用的关键力矩进行过程控制和结果追溯,全方位确保新能源产品的卓越品质。
创新不止,积极拥抱新技术变革
当新时代的数字化技术浪潮席卷全球,唯有通过数字化转型打造新型智慧工厂,让制造变得更“聪明”,方能在激烈竞争中脱颖而出。在构建覆盖全产品生命周期和制造全业务活动的工业大数据平台同时,奇瑞捷豹路虎还围绕5G技术、虚拟制造等等新兴融合型技术领域,加快前瞻性布局,进一步提升智能制造的数字化程度。
奇瑞捷豹路虎早在2019年就已经与中国联通江苏分公司达成战略合作,率先布局5G网络,赋能智能制造升级。双方在网络技术研究、应用研究和通信服务与企业信息化等方面展开合作,奇瑞捷豹路虎常熟工厂已经运用了双方围绕工业物联网深度合作的5G技术,将推动5G网络与造车工艺的结合,助力智能制造提质进阶。
为缩短项目工期,提高产出率,奇瑞捷豹路虎常熟工厂还应用了多项数字化仿真技术。通过离散事件仿真技术,在建立生产线之前,奇瑞捷豹路虎便可对生产节拍进行计算、验证生产能力,甚至在设计阶段验证产品的可行性。而在安装设备之前,凭借虚拟调试技术,奇瑞捷豹路虎可以先对机械及电气系统进行仿真评估,并在实施焊装工艺、涂装工艺前进行模拟仿真。通过诸多仿真技术的有效利用,奇瑞捷豹路虎大大降低了投产阶段的造车成本、零件损耗,也保障了交付时间与交付质量。
MR眼镜虚拟装配项目
作为国内首家中英合资高端汽车企业,奇瑞捷豹路虎积极响应提升企业数字化能力、数字经济和实体经济融合的发展方向,接下来将持之以恒,继续不断深化“智能+”的高质量发展方式,践行不断向中国市场提供全球一流品质的产品和服务的承诺。
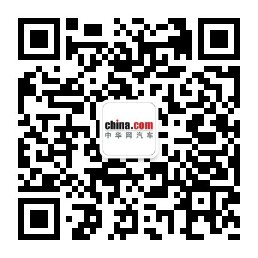